Power plant location | Salzbergen, Lower Saxony |
Power plant type | Thermal waste treatment plant |
Fuel | Municipal waste |
Output (net) | 47 MWth |
Incineration capacity | 130,000 t/a |
Steam generation | 360,000 t/a |
Efficiency | 85% |
Facts and figures
Steam from household waste
The core of the Salzbergen industrial concept is the construction and operation of the Salzbergen thermal waste treatment plant, TAS for short, by SRS EcoTherm GmbH, in which RWE Generation SE holds a 90% and H&R GmbH & Co. KGaA itself holds 10% of the shares.
Since 2004, TAS has been generating 360,000 tonnes of steam from an annual 130,000 tonnes of municipal waste. Travelling through an 800-m long pipeline, the steam reaches the industrial power plant, where it is initially used to produce electricity and then further utilised as process steam. Since 2018, the industrial power plant has been managed by SRS EcoTherm GmbH.
Constantly under full load
Since the TAS is constantly operating under full load, it delivers some two thirds of the steam required by the location. Peak demand is covered by one heavy-oil-fired and one natural-gas-fired steam generator in the industrial power plant. The natural-gas-fired steam generator and the back-pressure extraction turbine were installed as part of a 13 million euro investment in the plant in the years 2015 to 2017.
Energy concept with measurable benefits
For H&R ChemPharm, for the region and for the environment, the energy concept brings measurable benefits: the refinery can cut its annual energy supply costs. The fixed prices for steam deliveries over 30 years agreed with SRS EcoTherm also make production independent of price fluctuations on the energy market, thus offering a dependable calculation basis.
Modern technology minimises emissions
The Emsland district has secured low-cost removal of up to 70,000 tonnes of municipal waste annually. The remaining waste is delivered by several partners from the region. The emissions produced at the location from energy generation are reduced to a minimum thanks to the deployment of state-of-the-art combustion and flue gas scrubbing technology.

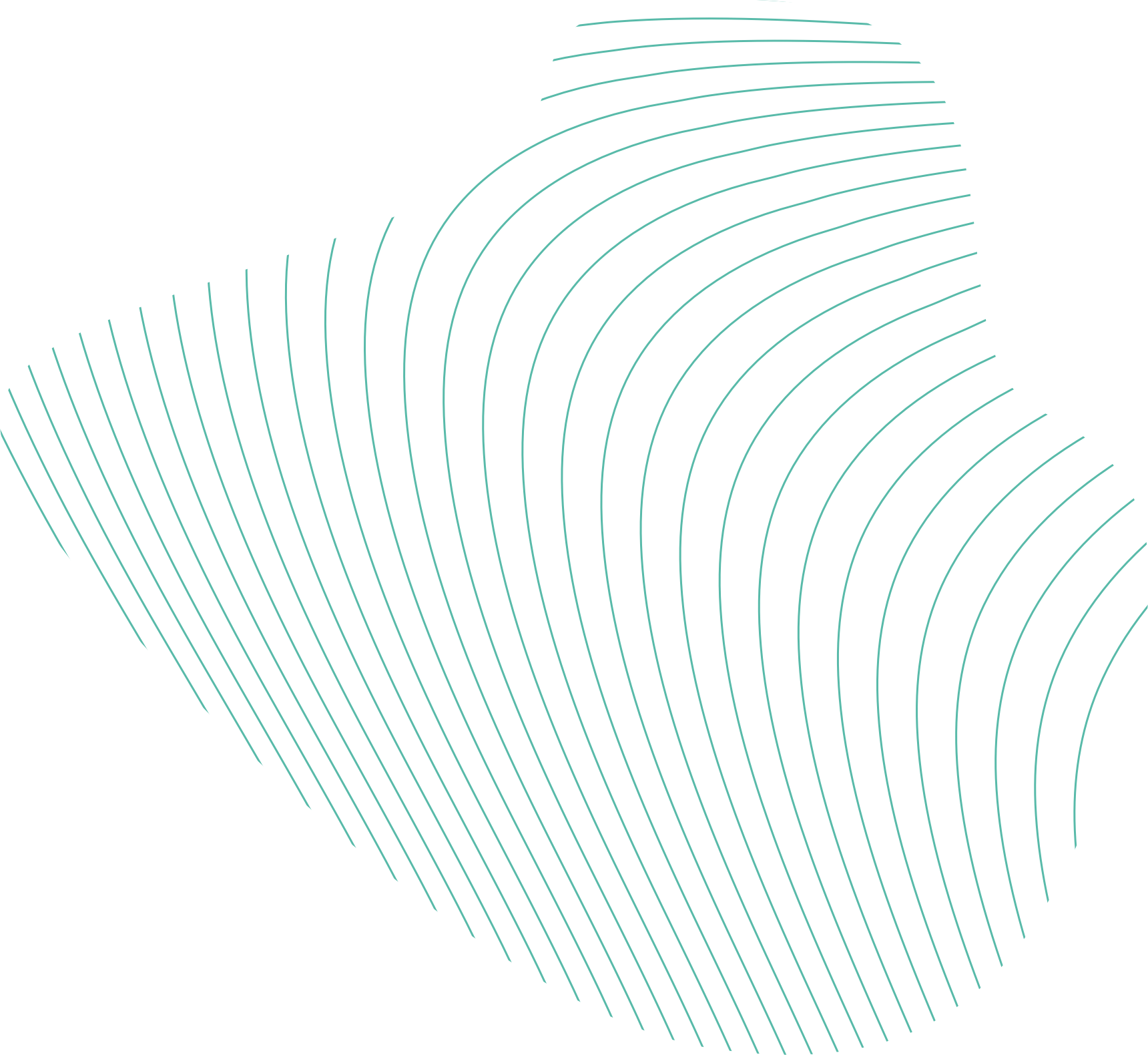